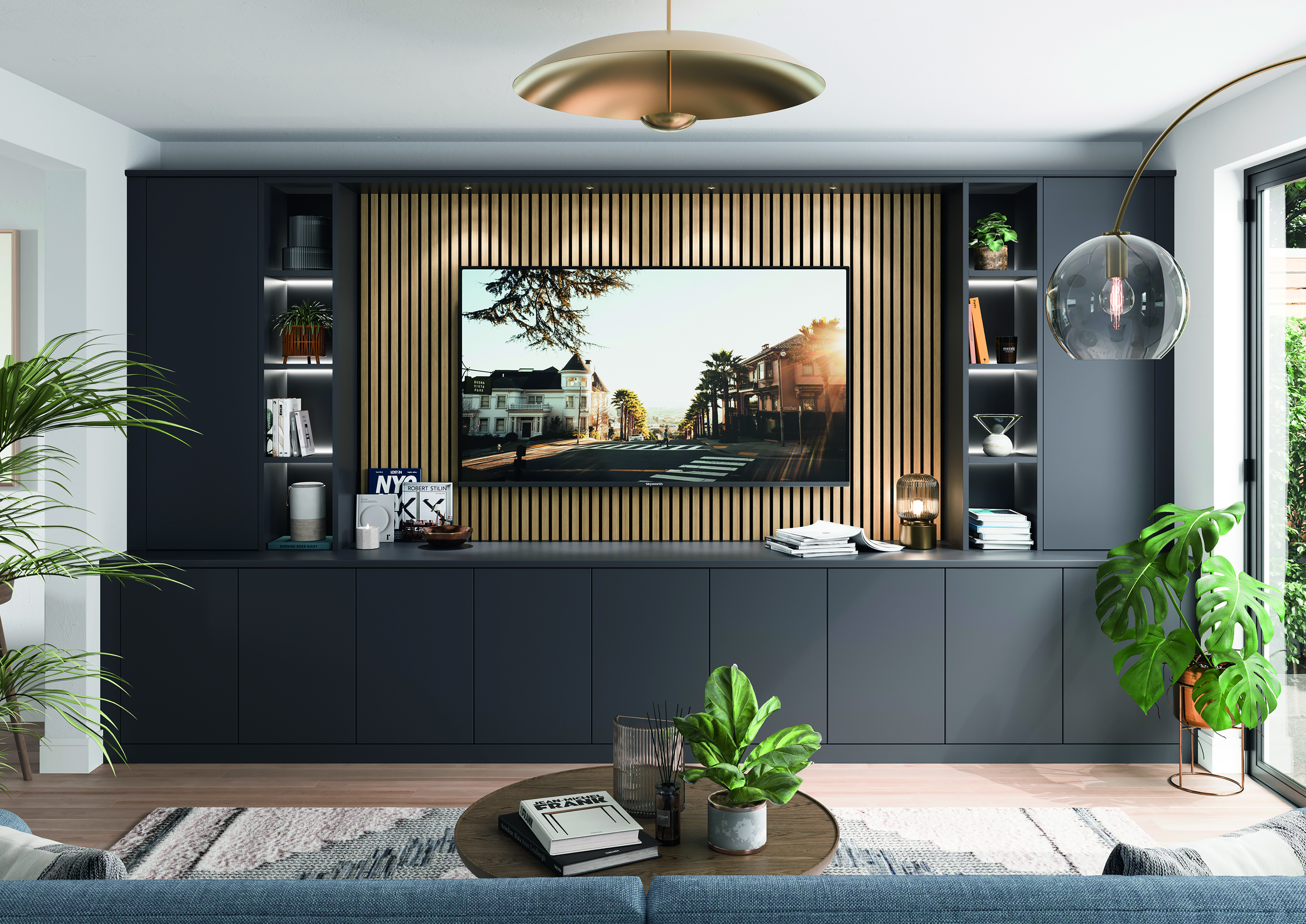
Following a company-wide ESG audit, furniture manufacturer Sharps has revolutionised the way it manages waste wood, by investing in processing in-house and partnering with leading wood based-panels manufacturer EGGER, to contribute to material circularity.
Sharps, the UK’s leading fitted bedroom furniture and wardrobes specialist, places emphasis on producing beautifully crafted and bespoke products with care for the environment, that includes the use of EGGER’s carbon neutral decorative faced chipboard in its production facilities.
As part of its ongoing commitment to sustainability, Sharps recently carried out an ESG audit, assisted by EGGER, which included waste analysis. The findings revealed that Sharps generated a significant amount of waste from MFC cut-offs during both its production and manufacturing processes.
As a result of the audit, Sharps began to look at more efficient ways of reducing the amount of waste generated and recycling it through waste service providers.
Speaking about the importance of sustainability, Peter Welsh, Operations Director at Sharps, said:
“As an industry leader and manufacturer, we really need to pay more attention to this. On a brand level, it is important that we do the right thing for our customers and for the planet. Our products are covered by a long guarantee, which shows they are truly designed and built to last. We have partnered with Forest Carbon to offset our carbon emissions, and we use renewable electricity in our showrooms. These are just some examples of how we are actively working to reduce our environmental impact.
“After researching the market and speaking with the EGGER team in Hexham, we decided to work with recycling and waste management specialist Timberpak (a subsidiary of EGGER UK), and Olivers Transport. This meant that our MFC off cuts would be collected, processed and then transported to EGGER to be reused in the production chipboard at their Hexham plant.
“This brought with it numerous benefits for us as a manufacturer and the wider industry. From a material circularity and environmental perspective, recycling the waste back into useable material for production is hugely positive. As well as helping to prolong the lifecycle of the product and reduce the amount of waste sent to landfill, it can preserve precious raw materials and store in captured CO2 for longer. It is also a more cost-effective process, when compared to the waste collection and removal fees we were previously paying.”
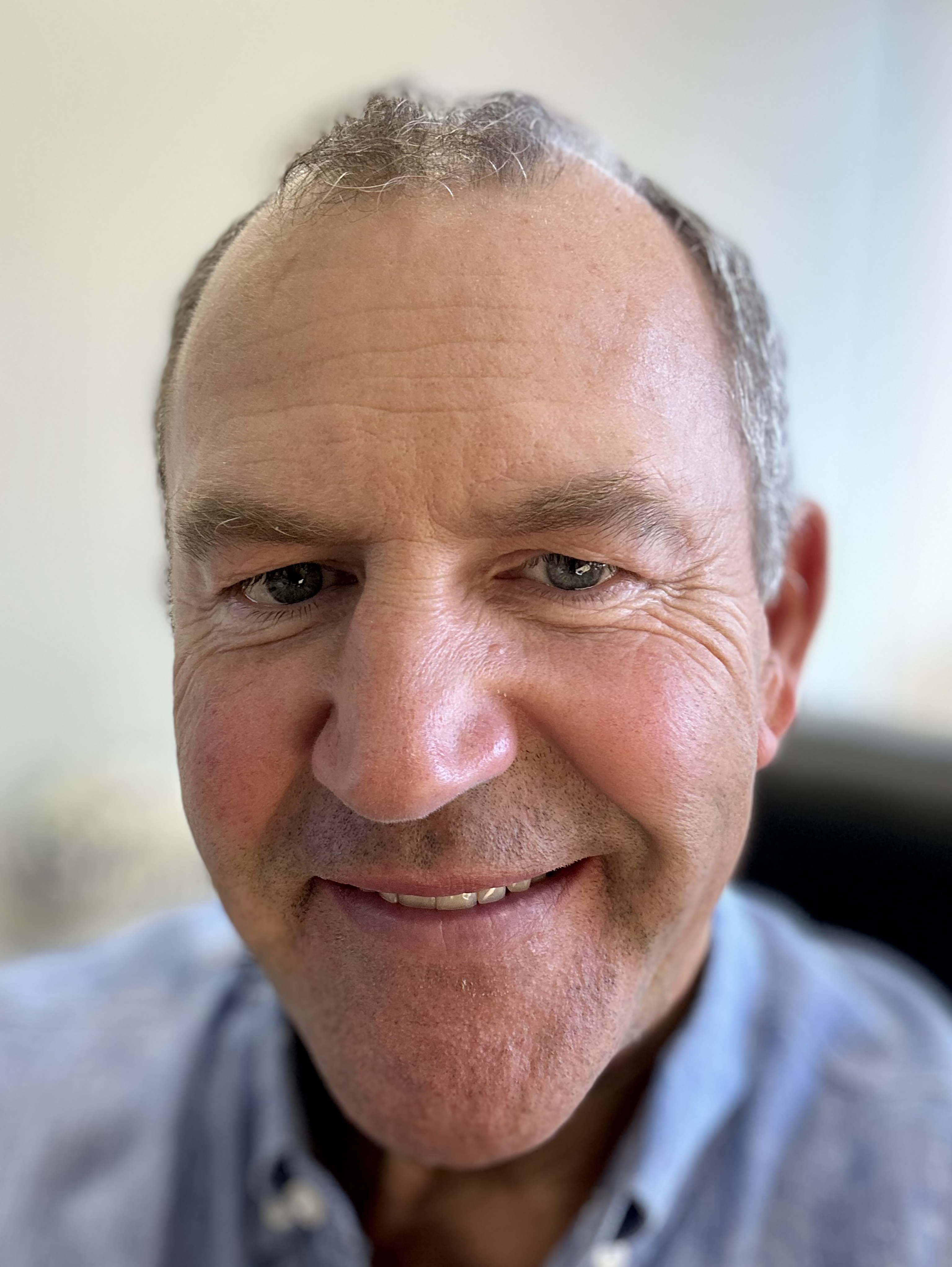
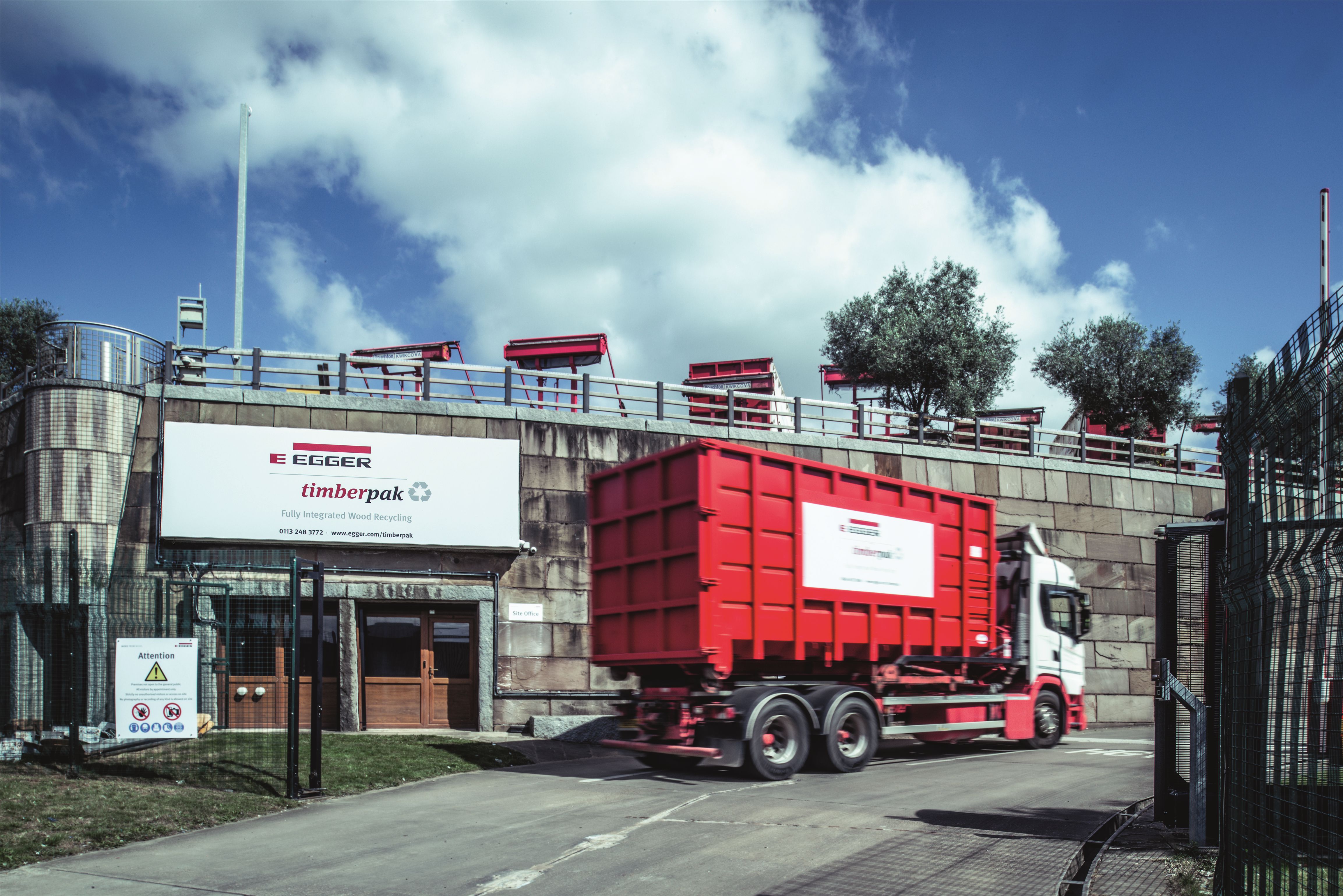
Sharps has now taken this one step further, installing a woodchipper on its Bilston site. This means any waste wood material is processed directly by Sharps before being collected and delivered to EGGER, helping to cut down on transport costs and ‘empty miles’.
Peter continued: “Historically, the waste timber material was collected in skips and then transported to various recycling centres at third party sites. Now, by processing the timber in-house, everything is more streamlined and the waste chips are far easier to store and transport than solid board off-cuts, meaning there are less lorries on the road.
“Wood is an incredibly valuable and natural commodity. As such, if through this initiative we can reduce the number of virgin trees being used in manufacturing, extend the lifecycle of our existing timber and use less transport, it can only be a positive. Indeed, if everyone were to recycle more, our planet and its inhabitants would all benefit.”
Mark Hayton, Head of Wood Purchasing at Timberpak, said:
“I believe it’s key to highlight the importance of the waste hierarchy in waste disposal; we need everyone to understand the value of wood as a resource and as such, ensure we use it fully before it is burned. We encourage collaboration to facilitate recycling and provide producers with outlets, all while promoting sustainable waste management practices.”
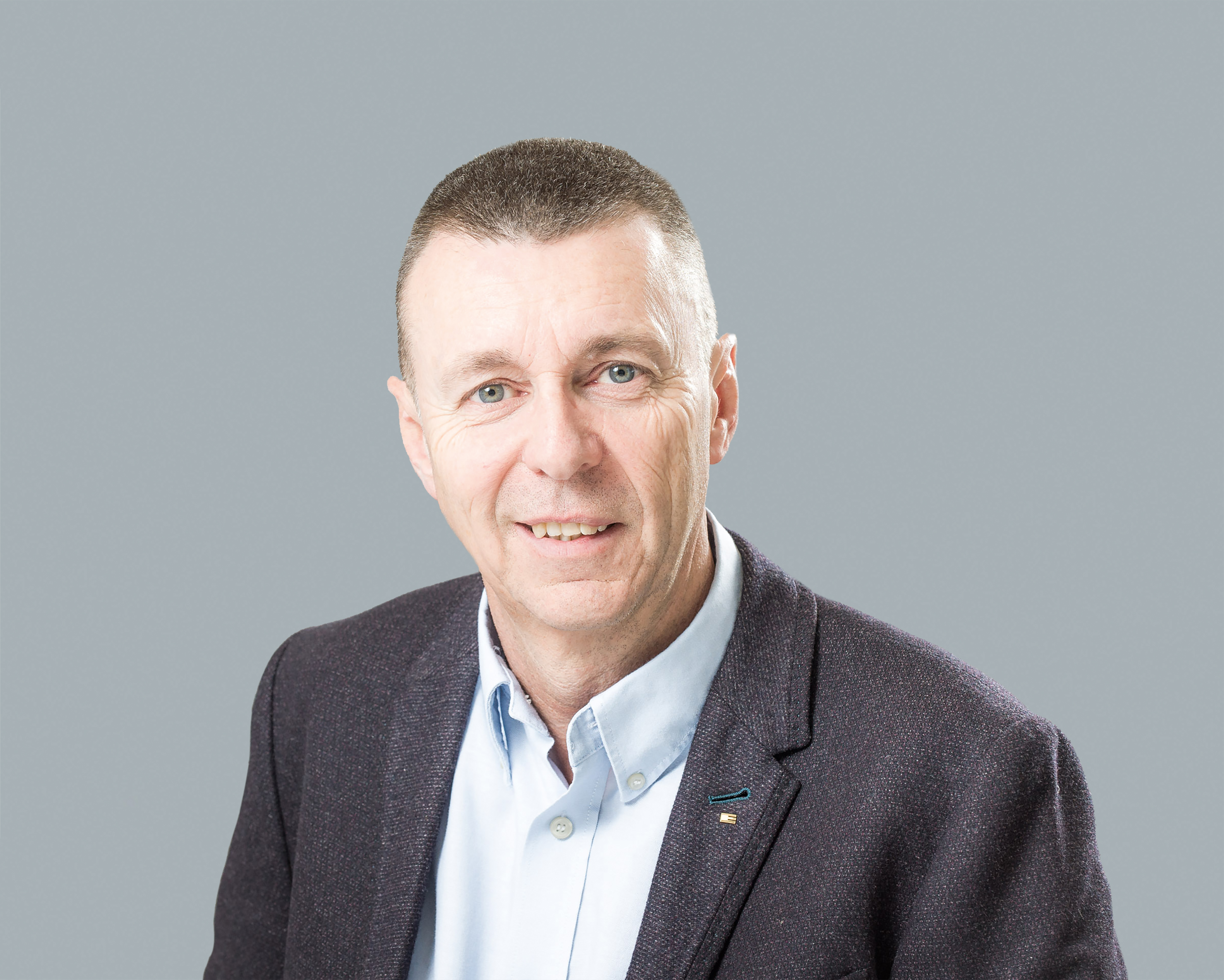
For EGGER, acting sustainably is more than mere a duty. Its main ambition is management with future generations in mind and recycling is a big part of that. EGGER’s board recipe reflects that commitment, as their UK MFC boards are made up of 45% recycled timber alongside 30% sawmill by-products and 25% roundwood.
For more information, please visit www.sharps.co.uk/ .