What exactly is value engineering in construction?
As cost pressures continue throughout the industry, it’s a term we expect to hear increasingly in interior design projects.
What does it actually mean?
To value engineer is to make savings on a project without compromising the design, performance or quality. Savings can be made not only in cost, but also in time and, increasingly, in environmental impact. This can take many forms.
A few examples of value engineering include:
- Selecting materials that optimise the efficiency of a design, in cost and time.
- Making intelligent switches from real materials to alternatives that positively impact the budget and the environment.
- Choosing materials that promote material circularity, utilise recycled material, or are recyclable at end of life.
- treamlining the fabrication process, reducing labour time and costs through considered product specification.
- Avoiding over-specification of materials that are more costly or technical than the application requires.
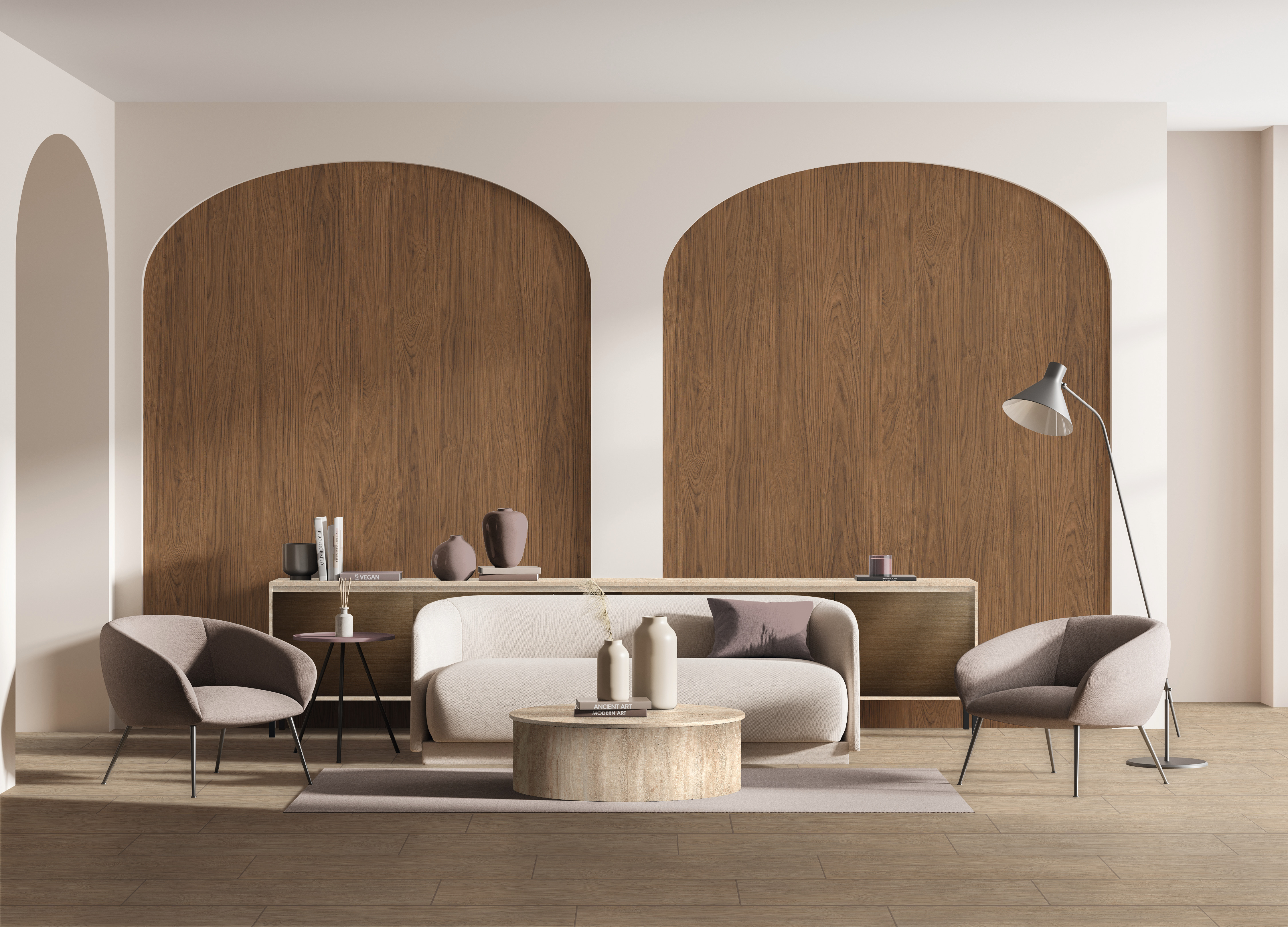
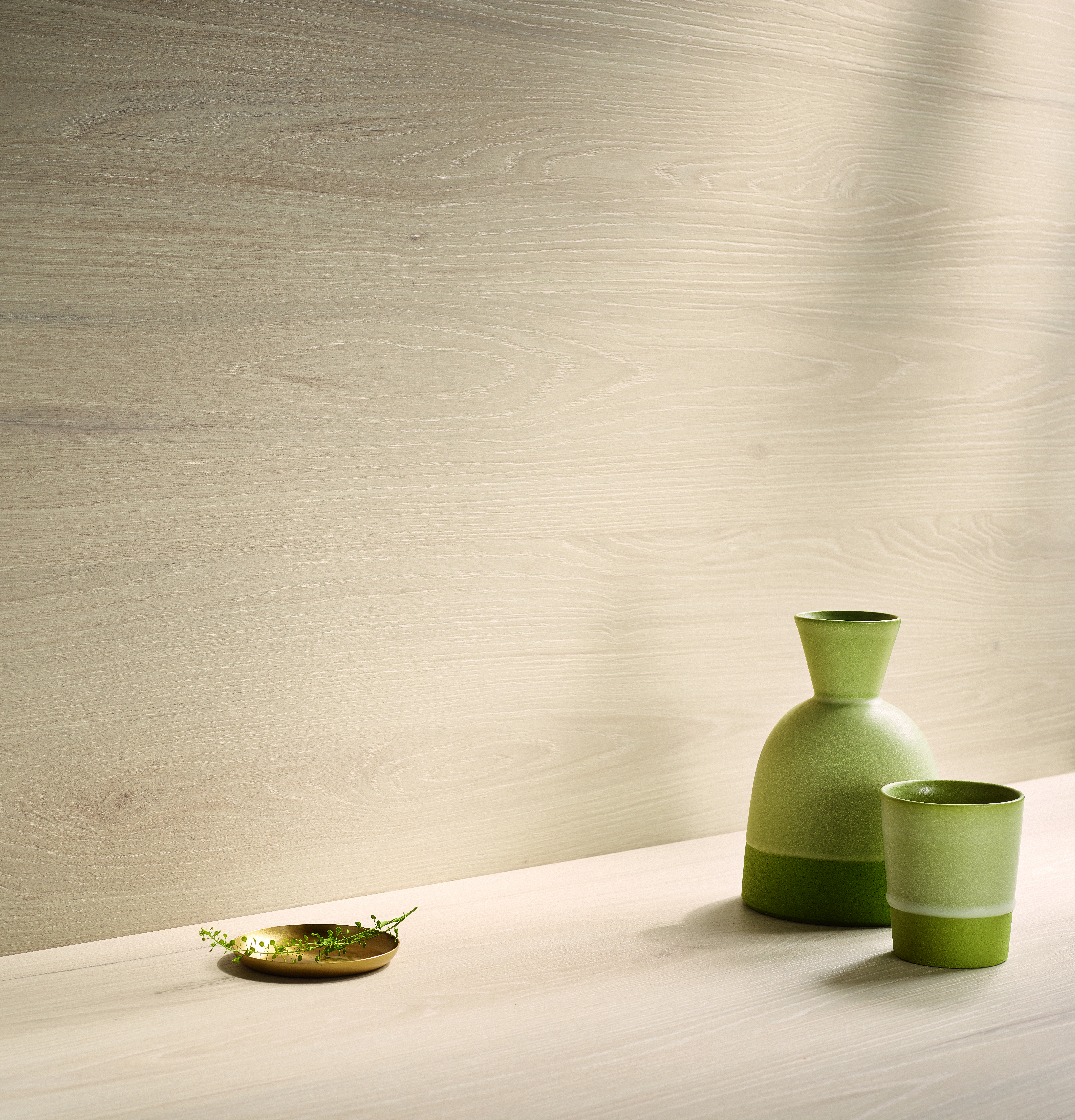
While these are some core aspects of value engineering, it is not ‘one size fits’ all.
When specifying EGGER materials in projects, our team of specification advisors will work with you to identify the individual needs of a project and offer tailored solutions.
How can designers implement value engineering in their projects?
One of the most effective tools in successful value engineering is a thorough understanding of materiality. Knowing the advantage, limitations, composition and origin of a material will ensure specification is relative to performance requirements, within environmental parameters, and on budget from the outset.
Let’s explore some examples.
Knowing material advantages and limitations.
Knowing the advantages and limitations of a material will ensure that specification is relative to performance requirements, but not beyond.
For example, one of the most common causes of missed value engineering opportunities comes from a confusion between laminate and decorative faced chipboard panels. This is understandable – a laminate, once bonded to a substrate such as chipboard, plywood or MDF, can be visually difficult to tell apart from a faced panel and service many of the same functions.
Similarly, the manufacturing process of making decorative faced panels is commonly known as ‘lamination’ across the industry. Despite this, laminate sheet material is not used in the manufacture of decorative faced panels. Instead, an impregnated decor paper layer is applied as a face to both sides of a wood based core, resulting in a panel material.
However, there are a number of core differences to keep in mind.
Laminate is a thin sheet material that requires bonding, using a balancer and a suitable substrate. All incur a cost. However, a main advantage of laminate is that its composition offers heightened resilience for areas facing more wear, making laminate ideal for restaurant table tops, reception desks, retail counters, bars and table tops.
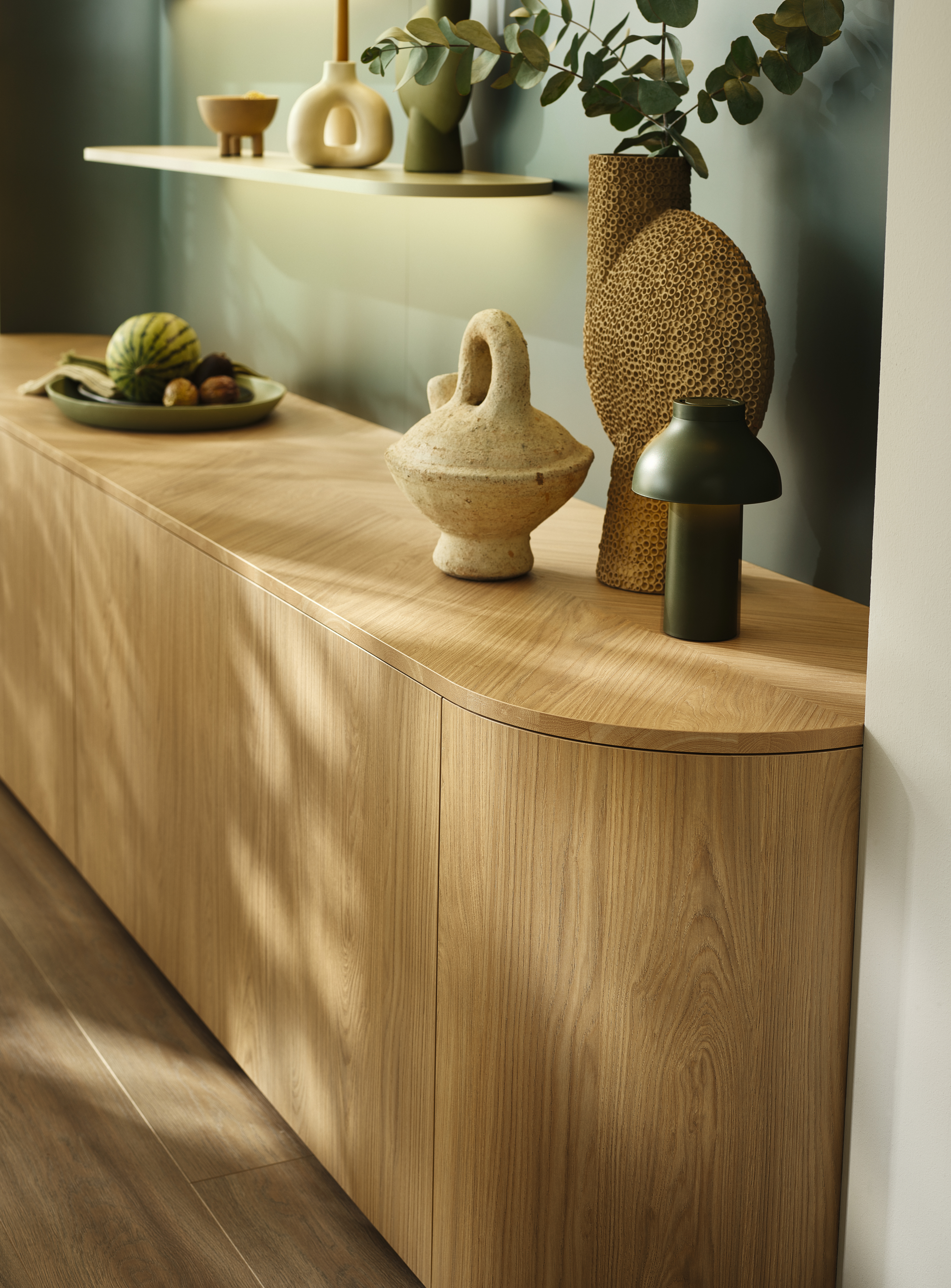
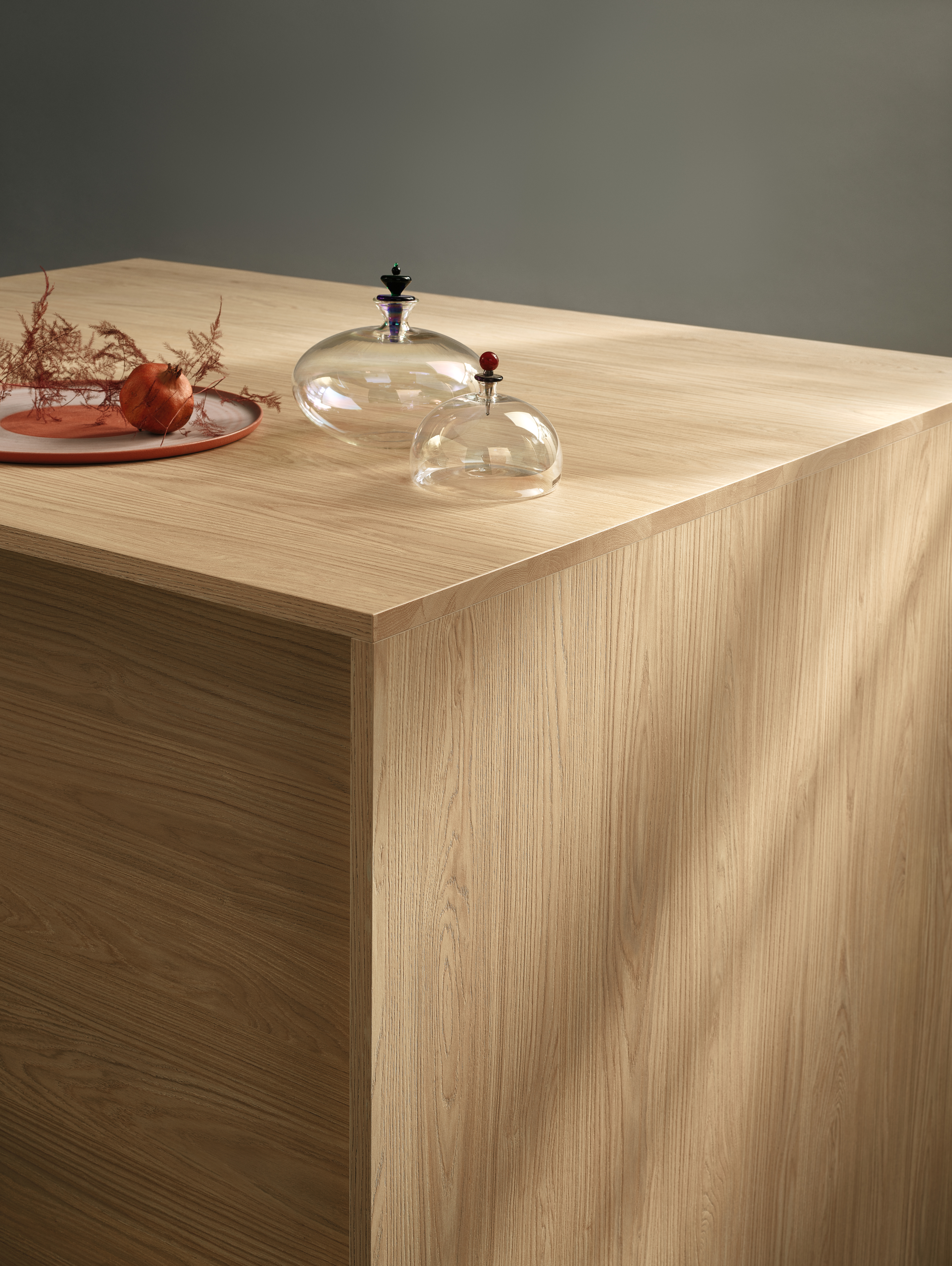
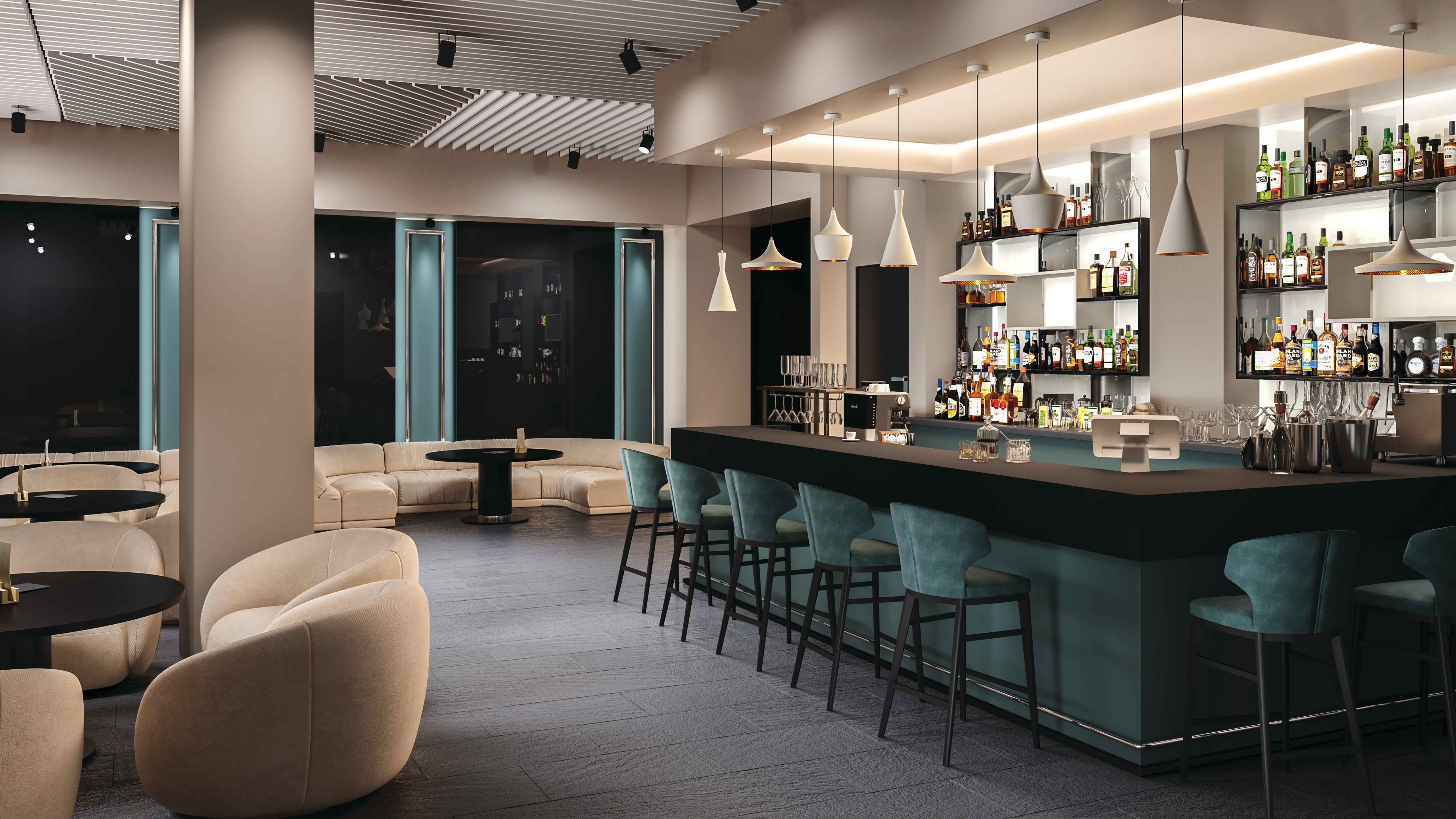
Decorative faced chipboard panels are supplied in a board format ready for cutting, removing the additional labour and material cost, but are engineered to withstand mid-traffic use as opposed to the high traffic resistance of laminate. Applications such as shelving and wall panelling see less surface traffic, so are most efficiently and economically fabricated in this material.
For a detailed breakdown of laminate, and the difference between laminate and decorative faced panels, see article: What is laminate and where should I specify it?
Effective value engineering can be implemented by using the same decorative finish in both materials, keeping material cost and labour controlled while maintaining coordinated design concepts.
Knowing material composition and origin.
Controlling the environmental impact of a project adds another level of value that is of increasing importance in the industry. This too can be achieved through effective material specification, more efficiently done with knowledge of the material composition and origin: what it is made from, how it is made, and what raw materials it contains.
On of the most common causes of missed value engineering opportunities in this area is a perceived connection between natural and environmentally sustainable, but this is not always the case. Many naturally derived materials, such as stone, marble or metal, require energy extensive processes, and carry substantial carbon footprints as a result of fabrication and transportation. Non-recyclability is often another factor.
Instead, pay attention to products that make use of recycled content and are recyclable at end of life, promoting material circularity. Manufacturers’ raw material procurement and production techniques should also be considered, and attention paid to supporting documentation available via websites and published resources. Always look for transparency on this topic.
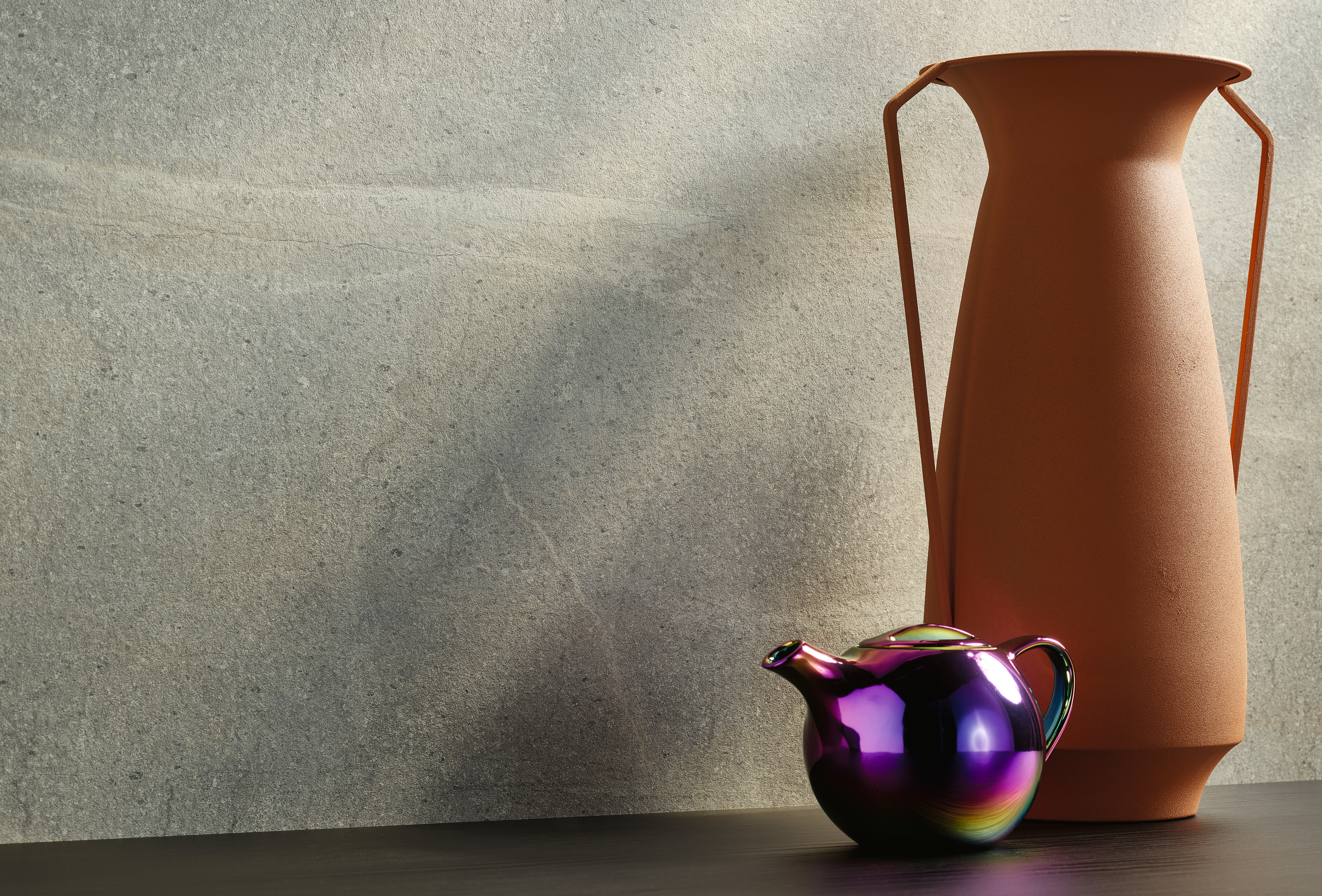
What are the benefits of value engineering projects?
We have discussed the potential for making savings in cost, delivery time or environmental impact, leading to a successfully value engineered design, that considered material specification can yield. A saving to any degree is a benefit
But when specifying for high volume projects, the cumulative benefits of value engineering can significantly impact the end result, both economically and environmentally, and in terms of the schedule.
Let’s look at an example of value engineering in action.
In their private residential development The Stage, Galliard Homes chose a decorative faced panel, EGGER Eurodekor Faced Chipboard, as an efficient and cost effective material solution for kitchen unit carcasses and frontals. This material sequesters carbon from the atmosphere to a value of 17.8kg co2e per square meter of material (based on 18mm thickness).
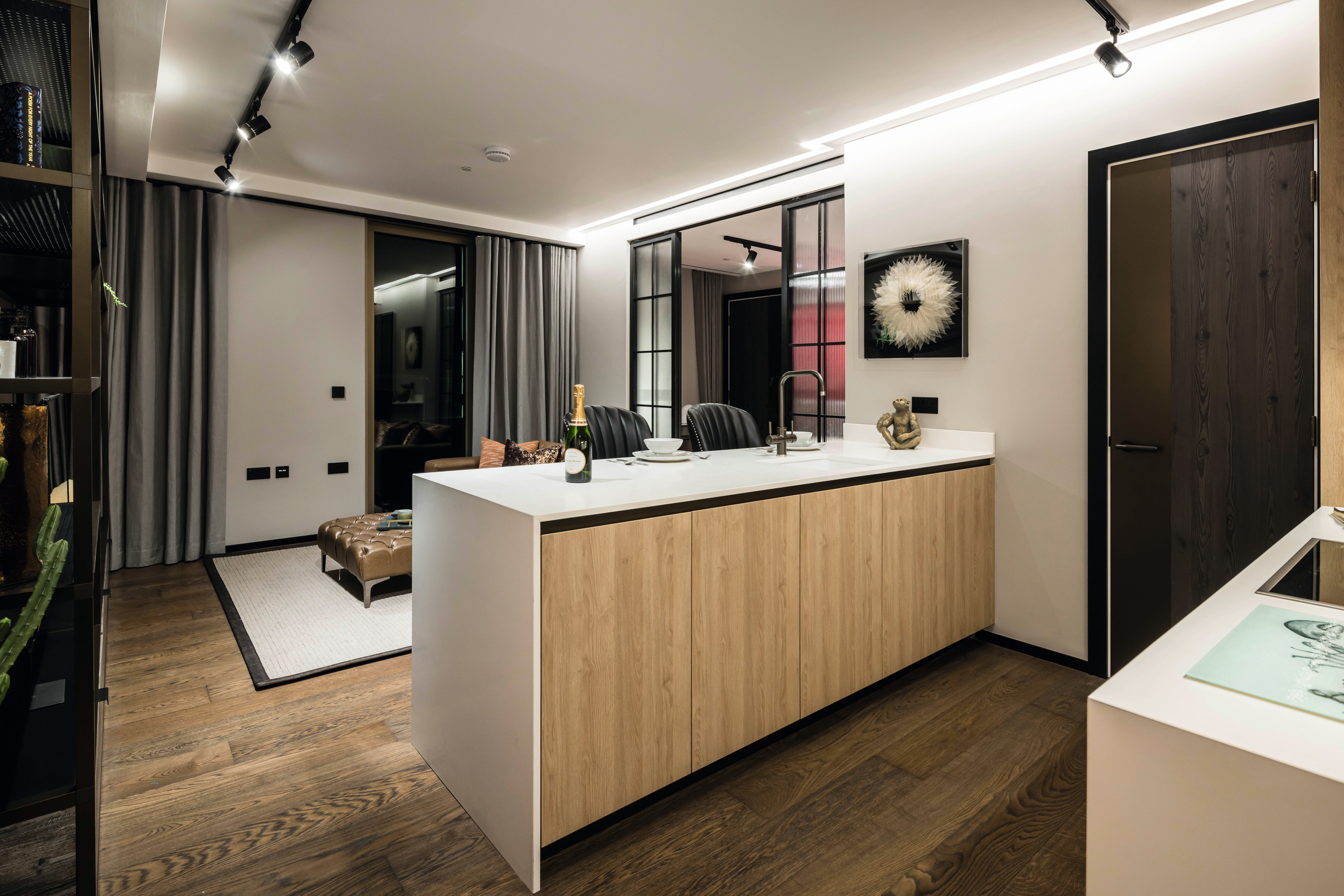
As a result, every apartment retains 567.428kg c02e in its kitchen units.
As a 412 unit development, The Stage retains over 233,780.501kg co2e in its kitchen units alone.
With this specification, the design team also chose a material that utilises recycled wood and by-product in its manufacture and is 100% recyclable at end of life, resulting in a considered material specification that allowed for significant reduction in environmental impact and costs without compromise on design.
Support
This article is for informational purposes only. If you are searching for the information about specific EGGER products, please visit our knowledge hub .